Turbochargers Can Be Fun For Anyone
Table of ContentsAn Unbiased View of TurbochargersMore About Turbochargers4 Simple Techniques For Turbochargers
Modern turbochargers can utilize wastegates, blow-off valves and variable geometry, as discussed in later areas. In gas engine turbocharger applications, increase pressure is restricted to keep the entire engine system, including the turbocharger, inside its thermal and mechanical design operating range (turbochargers). Over-boosting an engine often triggers damage to the engine in a variety of ways consisting of pre-ignition, getting too hot, and over-stressing the engine's internal hardware.Opening the wastegate permits the excess energy predestined for the turbine to bypass it and pass directly to the exhaust pipe, therefore reducing increase pressure. The wastegate can be either managed by hand (regularly seen in airplane) or by an actuator (in automobile applications, it is frequently controlled by the engine control unit).

The increased temperature from the higher pressure offers a greater Carnot effectiveness. A minimized density of consumption air is brought on by the loss of atmospheric density seen with elevated elevations. Thus, a natural usage of the turbocharger is with airplane engines. As an aircraft climbs up to greater altitudes, the pressure of the surrounding air quickly falls off.
In aircraft engines, turbocharging is commonly used to preserve manifold pressure as elevation boosts (i. e. to compensate for lower-density air at greater elevations). Given that air pressure lowers as the aircraft climbs, power drops as a function of altitude in usually aspirated engines. Systems that utilize a turbocharger to maintain an engine's sea-level power output are called turbo-normalized systems.

5 inHg (100 kPa). Turbocharger lag (turbo lag) is the time required to change power output in response to a throttle change, noticed as a doubt or slowed when speeding up as compared to a naturally aspirated engine. This is due to the time needed for the exhaust system and turbocharger to generate the required boost which can also be described as spooling.
Little Known Facts About Turbochargers.
Superchargers do not suffer this issue, due to the fact that the turbine is gotten rid of due to the compressor being straight powered by the engine. Turbocharger applications can be categorized into those that require modifications in output power (such as vehicle) and see this website those that do not (such as marine, airplane, business automotive, industrial, engine-generators, and engines).
Engine develops minimize lag in a variety of methods: Decreasing the rotational inertia of the turbocharger by utilizing lower radius parts and ceramic and other lighter materials Changing the turbine's aspect ratio Increasing upper-deck atmospheric pressure (compressor discharge) and improving wastegate action Lowering bearing frictional losses, e. g., using a foil bearing instead of a standard oil bearing Utilizing variable-nozzle or twin-scroll turbochargers Decreasing the volume of the upper-deck piping Utilizing multiple turbochargers sequentially or in parallel Utilizing an antilag system Using a turbocharger spool valve to increase exhaust gas flow speed to the (twin-scroll) turbine Often turbo lag is mistaken for engine speeds that are below increase limit.
This await lorry speed boost is not turbo lag, it is inappropriate gear selection for boost need. turbochargers. When the vehicle reaches adequate speed to provide the required rpm to reach boost threshold, there will be a far shorter hold-up while the turbo itself develops rotational energy and transitions to positive boost, only this last part of the hold-up in attaining favorable boost is the turbo lag.
Below a certain rate of circulation, a compressor produces irrelevant increase. This restricts increase at a particular RPM, regardless of exhaust gas pressure. More recent turbocharger and engine developments have actually gradually decreased increase thresholds. Electrical boosting (" E-boosting") is a brand-new innovation under advancement. It uses an electrical motor to bring the turbocharger as much as operating speed quicker than possible utilizing available exhaust gases.
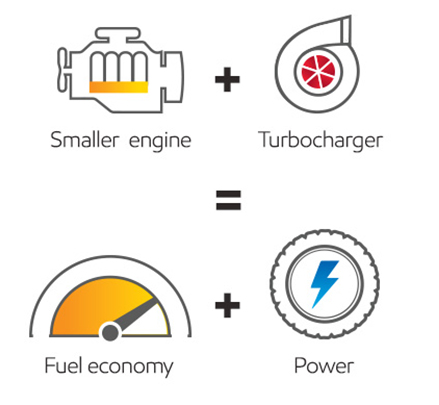
The running speed (rpm) at which there is adequate exhaust go to my site gas momentum to compress the air entering into the engine is called the "increase threshold rpm". Reducing the "increase threshold rpm" can enhance throttle reaction - turbochargers. The turbocharger has three main elements: The turbine, which is practically always a radial inflow turbine (however is generally a single-stage axial inflow turbine in large Diesel motor) The compressor, which is often a centrifugal compressor The center housing/hub rotating assembly Numerous turbocharger installations utilize additional innovations, such as wastegates, intercooling and blow-off valves.
The Facts About Turbochargers Uncovered
On the right are the braided oil supply line and water coolant line connections. Compressor impeller side with the cover removed. Turbine side real estate got rid of. Energy attended to the turbine work is transformed from the enthalpy and kinetic energy of the gas. The turbine housings direct the gas flow through the turbine as it spins at approximately 250,000 rpm.
Often the very same basic turbocharger assembly is available from the producer with numerous housing choices for the turbine, and in important link some cases the compressor cover as well. This lets the balance in between performance, reaction, and performance be customized to the application. The turbine and impeller wheel sizes likewise determine the quantity of air or exhaust that can flow through the system, and the relative efficiency at which they run.
Measurements and shapes can vary, along with curvature and variety of blades on the wheels. A turbocharger's efficiency is closely tied to its size. Large turbochargers take more heat and pressure to spin the turbine, producing lag at low speed. Small turbochargers spin rapidly, however might not have the very same efficiency at high acceleration.